The Latest from Delta Farm Press
Ducks in Rice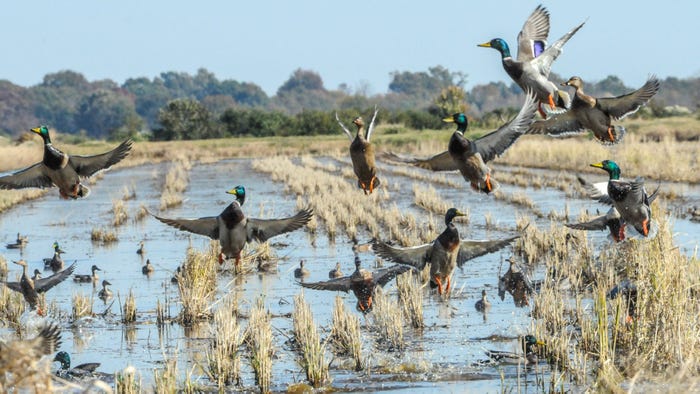
Conservation & Sustainability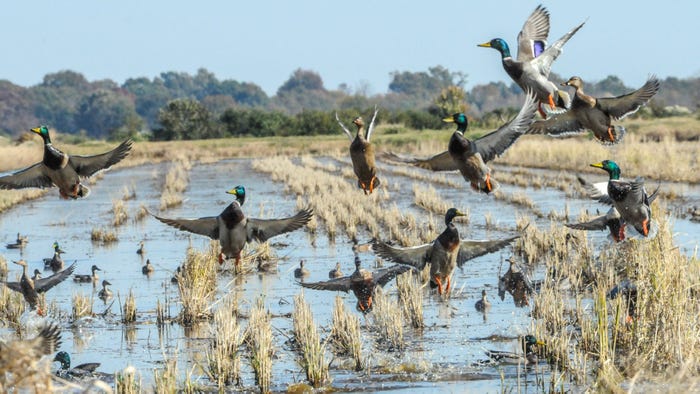
Waterfowl and Delta agriculture, upcoming eventWaterfowl and Delta agriculture, upcoming event
CTIC, Ducks Unlimited partner to host conservation workshop.
Market Overview
Contract | Last | Change | High | Low | Open | Last Trade |
---|---|---|---|---|---|---|
Jul 24 Corn | 459.5 | -7.5 | 467 | 458.75 | 467 | 02:52 PM |
Jul 24 Oats | 397.25 | -2.25 | 403 | 394 | 394 | 02:48 PM |
Jun 24 Class III Milk | 19.62 | +0.19 | 19.66 | 19.45 | 19.45 | 02:52 PM |
Jul 24 Soybean | 1238.5 | -8 | 1248 | 1231.25 | 1244 | 02:53 PM |
Aug 24 Feeder Cattle | 254.05 | -0.375 | 254.95 | 253.075 | 254.725 | 02:53 PM |
Jun 24 Ethanol Futures | 2.161 | unch — | 2.161 | 2.161 | 2.161 | 09:37 PM |

Copyright © 2019. All market data is provided by Barchart Solutions.
Futures: at least 10 minute delayed. Information is provided ‘as is’ and solely for informational purposes, not for trading purposes or advice.
To see all exchange delays and terms of use, please see disclaimer.
All Delta Farm Press
Subscribe to receive top agriculture news
Be informed daily with these free e-newsletters