The Latest from Delta Farm Press
Jamie and Chad Daniel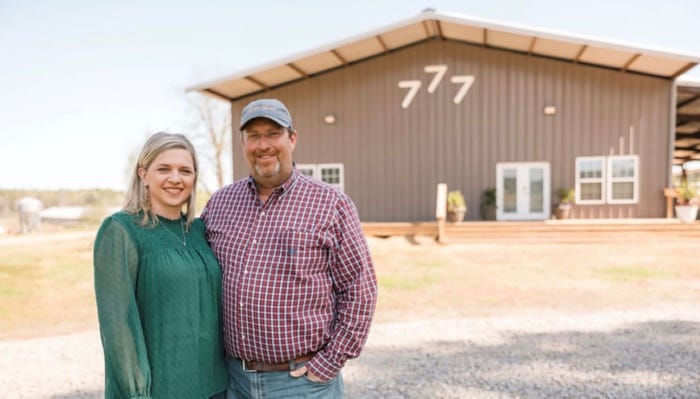
Farm Life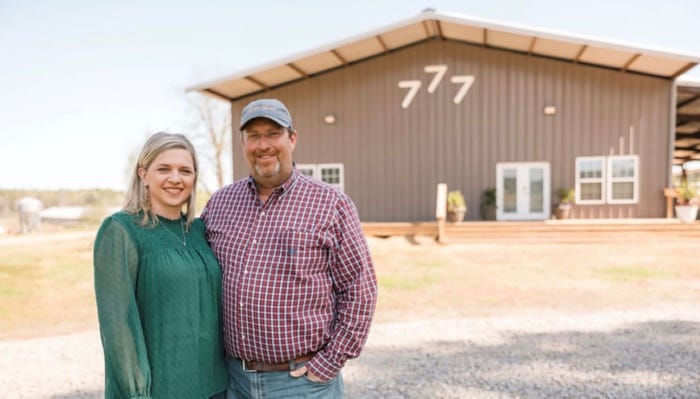
Jamie Daniel: Women on the farmJamie Daniel: Women on the farm
Education, networking, and leadership experiences provide new opportunities for women in agriculture.
Market Overview
Contract | Last | Change | High | Low | Open | Last Trade |
---|---|---|---|---|---|---|
Jul 24 Corn | 451.75 | -0.25 | 453 | 451.5 | 451.75 | 08:07 AM |
Jul 24 Oats | 355.25 | +4.25 | 356.75 | 352.25 | 352.25 | 07:39 AM |
May 24 Class III Milk | 18.25 | +0.07 | 18.28 | 18.25 | 18.28 | 04:21 AM |
Jul 24 Soybean | 1175.5 | -4.25 | 1181 | 1175.5 | 1179 | 08:07 AM |
Aug 24 Feeder Cattle | 258.3 | +2 | 258.8 | 254.25 | 256.425 | 06:04 PM |
May 24 Ethanol Futures | 2.161 | unch — | 2.161 | 2.161 | 2.161 | 09:38 PM |

Copyright © 2019. All market data is provided by Barchart Solutions.
Futures: at least 10 minute delayed. Information is provided ‘as is’ and solely for informational purposes, not for trading purposes or advice.
To see all exchange delays and terms of use, please see disclaimer.
All Delta Farm Press
Subscribe to receive top agriculture news
Be informed daily with these free e-newsletters